Łączenie dwóch kompresorów może być istotnym krokiem w zwiększeniu wydajności systemu pneumatycznego. Warto zacząć od zrozumienia, jakie są różnice między kompresorami oraz jakie mają zastosowania. Kompresory mogą być używane do różnych celów, takich jak zasilanie narzędzi pneumatycznych, napełnianie zbiorników czy też w procesach przemysłowych. Kluczowym aspektem przy łączeniu kompresorów jest ich typ oraz sposób, w jaki będą ze sobą współpracować. Można zdecydować się na połączenie równoległe lub szeregowe, co wpływa na ciśnienie i przepływ powietrza. W przypadku połączenia równoległego oba kompresory pracują jednocześnie, co pozwala na zwiększenie wydajności bez podnoszenia ciśnienia. Z kolei połączenie szeregowe umożliwia uzyskanie wyższego ciśnienia, ale wymaga staranności w doborze odpowiednich modeli.
Jakie są najlepsze metody łączenia kompresorów?
Wybór metody łączenia kompresorów zależy od wielu czynników, takich jak ich specyfikacje techniczne oraz zamierzony cel użycia. Jednym z najczęściej stosowanych sposobów jest połączenie równoległe, które pozwala na efektywne wykorzystanie mocy obu urządzeń. W takim układzie każdy z kompresorów działa niezależnie, co oznacza, że w przypadku awarii jednego z nich drugi nadal będzie funkcjonował. To rozwiązanie jest szczególnie korzystne w środowiskach przemysłowych, gdzie ciągłość pracy jest kluczowa. Alternatywnie, połączenie szeregowe sprawdza się w sytuacjach, gdzie wymagana jest większa moc i ciśnienie. W tym przypadku jeden kompresor działa jako podstawa dla drugiego, co może prowadzić do lepszego wykorzystania zasobów energetycznych. Ważne jest również odpowiednie dobranie elementów instalacji, takich jak zawory czy przewody, które muszą być dostosowane do specyfiki obu urządzeń.
Jakie są najczęstsze problemy przy łączeniu kompresorów?
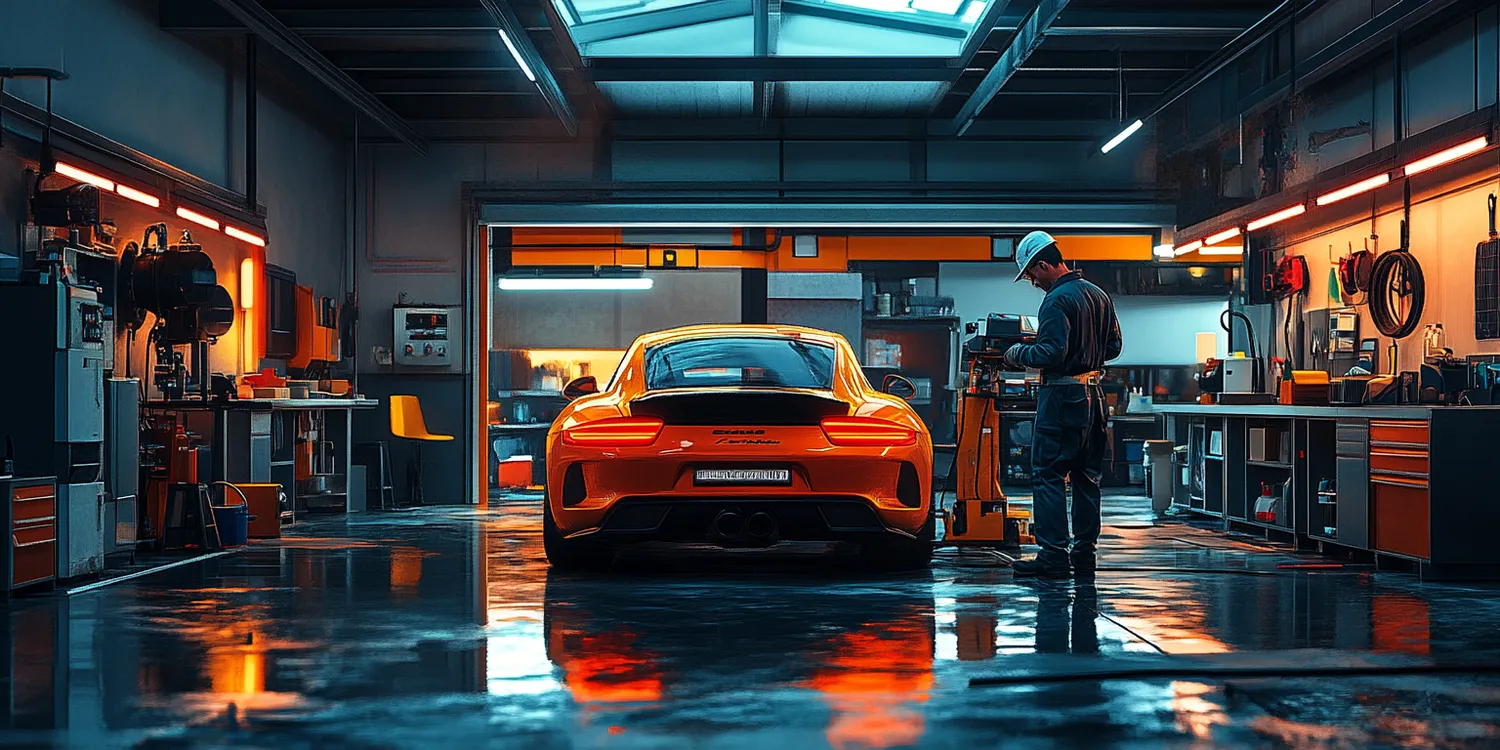
Podczas łączenia dwóch kompresorów mogą wystąpić różnorodne problemy techniczne, które warto przewidzieć i rozwiązać jeszcze przed rozpoczęciem pracy. Jednym z najczęstszych wyzwań jest niewłaściwe dopasowanie parametrów obu urządzeń. Różnice w ciśnieniu roboczym czy wydajności mogą prowadzić do nieefektywnej pracy całego systemu. Kolejnym problemem może być niewłaściwe okablowanie lub instalacja przewodów pneumatycznych, co może skutkować wyciekami powietrza lub uszkodzeniem sprzętu. Ważne jest także monitorowanie temperatury pracy kompresorów; przegrzewanie się jednego z nich może prowadzić do awarii i przestojów w produkcji. Dodatkowo warto zwrócić uwagę na systemy zabezpieczeń i automatyki, które mogą pomóc w zarządzaniu pracą obu urządzeń oraz minimalizowaniu ryzyka wystąpienia awarii.
Jakie korzyści płyną z łączenia kompresorów?
Łączenie dwóch kompresorów niesie ze sobą wiele korzyści zarówno dla użytkowników indywidualnych, jak i dla przedsiębiorstw przemysłowych. Przede wszystkim zwiększa to ogólną wydajność systemu pneumatycznego poprzez umożliwienie jednoczesnej pracy obu urządzeń. Dzięki temu można osiągnąć większy przepływ powietrza lub wyższe ciśnienie robocze, co ma kluczowe znaczenie w wielu zastosowaniach przemysłowych. Połączenie kompresorów pozwala również na lepsze zarządzanie kosztami energii; jeśli jeden z kompresorów nie jest potrzebny, można go wyłączyć bez wpływu na działanie całego systemu. Dodatkowo elastyczność takiego rozwiązania umożliwia łatwiejszą adaptację do zmieniających się potrzeb produkcyjnych czy projektowych. Użytkownicy mogą także liczyć na dłuższą żywotność sprzętu dzięki mniejszemu obciążeniu poszczególnych jednostek oraz możliwości ich rotacyjnego użytkowania.
Jakie są kluczowe elementy do rozważenia przy łączeniu kompresorów?
Przy łączeniu dwóch kompresorów istnieje wiele kluczowych elementów, które należy wziąć pod uwagę, aby zapewnić ich efektywne i bezpieczne działanie. Przede wszystkim ważne jest, aby oba kompresory miały zbliżone parametry techniczne, takie jak ciśnienie robocze oraz wydajność. Różnice w tych parametrach mogą prowadzić do nieefektywnej pracy systemu i potencjalnych uszkodzeń. Kolejnym istotnym aspektem jest dobór odpowiednich akcesoriów, takich jak zawory, manometry czy przewody pneumatyczne. Właściwe komponenty powinny być dostosowane do specyfiki obu urządzeń, aby uniknąć problemów z przepływem powietrza i ciśnieniem. Niezwykle ważne jest również zapewnienie odpowiedniej wentylacji dla kompresorów, aby zapobiec ich przegrzewaniu się. Warto również zastanowić się nad systemem monitorowania pracy urządzeń, który pozwoli na bieżąco kontrolować ich wydajność oraz stan techniczny.
Jakie są różnice między kompresorami tłokowymi a śrubowymi?
Wybór odpowiedniego typu kompresora ma kluczowe znaczenie dla efektywności całego systemu pneumatycznego. Kompresory tłokowe są jednymi z najpopularniejszych rozwiązań stosowanych w małych warsztatach i domowych zastosowaniach. Charakteryzują się prostą budową oraz stosunkowo niskimi kosztami zakupu. Działają na zasadzie sprężania powietrza za pomocą ruchomego tłoka, co może prowadzić do większych wahań ciśnienia. Z kolei kompresory śrubowe są bardziej zaawansowanymi urządzeniami, które oferują stabilniejsze ciśnienie robocze oraz wyższą wydajność. Dzięki zastosowaniu technologii śrubowej, te kompresory są w stanie pracować dłużej bez przerw na chłodzenie, co czyni je idealnym rozwiązaniem dla przemysłu. Warto również zauważyć, że kompresory śrubowe zazwyczaj generują mniej hałasu i wymagają mniejszej konserwacji niż ich tłokowe odpowiedniki.
Jakie narzędzia będą potrzebne do połączenia kompresorów?
Łączenie dwóch kompresorów wymaga odpowiednich narzędzi oraz materiałów, które zapewnią skuteczną i bezpieczną instalację. Na początek warto przygotować zestaw podstawowych narzędzi ręcznych, takich jak klucze płaskie i nasadowe, które będą niezbędne do montażu zaworów i połączeń pneumatycznych. Dobrze jest mieć także wkrętaki o różnych końcówkach oraz szczypce do zaciskania przewodów. Kolejnym istotnym elementem są przewody pneumatyczne; powinny być one dostosowane do ciśnienia roboczego oraz średnicy złączek obu kompresorów. Warto również zaopatrzyć się w manometry, które umożliwią monitorowanie ciśnienia w systemie oraz zawory bezpieczeństwa, które zabezpieczą układ przed nadmiernym ciśnieniem. Dodatkowo przydatne mogą okazać się uszczelki oraz taśmy teflonowe do uszczelniania połączeń gwintowanych.
Jakie są najlepsze praktyki przy konserwacji połączonych kompresorów?
Aby zapewnić długotrwałe działanie połączonych kompresorów, niezwykle istotna jest regularna konserwacja oraz przegląd techniczny urządzeń. Kluczowym krokiem jest regularne sprawdzanie poziomu oleju w kompresorach tłokowych oraz jego wymiana zgodnie z zaleceniami producenta. W przypadku kompresorów śrubowych należy zwrócić uwagę na filtry powietrza i oleju; ich czyszczenie lub wymiana powinna odbywać się zgodnie z harmonogramem serwisowym. Ważne jest również monitorowanie temperatury pracy urządzeń; przegrzewanie może prowadzić do szybszego zużycia komponentów oraz awarii. Regularne inspekcje układu pneumatycznego pozwolą na wykrycie ewentualnych wycieków powietrza czy uszkodzeń przewodów przed ich eskalacją. Dodatkowo warto prowadzić dziennik serwisowy, w którym będą zapisywane wszystkie wykonane prace konserwacyjne oraz obserwacje dotyczące pracy urządzeń.
Jakie są koszty związane z łączeniem kompresorów?
Koszty związane z łączeniem dwóch kompresorów mogą się znacznie różnić w zależności od wielu czynników, takich jak typ używanych urządzeń, konieczność zakupu dodatkowych akcesoriów czy też koszty robocizny związane z instalacją systemu. Na początku warto uwzględnić cenę samych kompresorów; jeśli planujemy zakup nowych modeli, ich cena może wynosić od kilku tysięcy złotych do kilkunastu tysięcy złotych za bardziej zaawansowane urządzenia. Dodatkowo należy doliczyć koszty związane z materiałami eksploatacyjnymi takimi jak przewody pneumatyczne, zawory czy manometry; te elementy mogą kosztować od kilkuset do kilku tysięcy złotych w zależności od jakości i specyfikacji technicznych. Koszty robocizny mogą być również znaczące; jeśli zdecydujemy się na zatrudnienie specjalisty do wykonania instalacji, warto przygotować się na dodatkowe wydatki rzędu kilku stówek lub więcej w zależności od skomplikowania projektu.
Jakie są zalety korzystania z profesjonalnych usług przy łączeniu kompresorów?
Korzystanie z profesjonalnych usług przy łączeniu kompresorów może przynieść wiele korzyści zarówno dla użytkowników indywidualnych, jak i dla firm przemysłowych. Przede wszystkim doświadczeni specjaliści posiadają wiedzę oraz umiejętności niezbędne do prawidłowego zaprojektowania i wykonania instalacji pneumatycznej. Dzięki temu można uniknąć wielu potencjalnych problemów związanych z niewłaściwym doborem komponentów czy błędami montażowymi. Profesjonalna obsługa gwarantuje również przestrzeganie wszystkich norm bezpieczeństwa oraz regulacji prawnych związanych z eksploatacją sprzętu pneumatycznego. Dodatkowo korzystając z usług fachowców można liczyć na doradztwo w zakresie wyboru najlepszych rozwiązań technologicznych oraz optymalizacji kosztów eksploatacyjnych systemu.