Destylator przemysłowy to urządzenie, które odgrywa kluczową rolę w wielu procesach produkcyjnych, zwłaszcza w przemyśle chemicznym oraz petrochemicznym. Jego głównym zadaniem jest oddzielanie substancji na podstawie różnic w temperaturze wrzenia. Proces ten polega na podgrzewaniu cieczy do momentu, w którym zaczyna ona parować, a następnie schładzaniu pary, aby skondensować ją z powrotem do stanu ciekłego. W praktyce oznacza to, że destylatory są wykorzystywane do produkcji alkoholu, oczyszczania wody, a także wytwarzania różnych chemikaliów. W zależności od zastosowania, destylatory mogą mieć różne konstrukcje i rozmiary, od małych jednostek laboratoryjnych po ogromne instalacje przemysłowe. Warto również zauważyć, że istnieją różne rodzaje destylacji, takie jak destylacja prosta, frakcyjna czy też destylacja azeotropowa, które są dostosowane do specyficznych potrzeb produkcyjnych.
Jakie są kluczowe elementy budowy destylatora przemysłowego
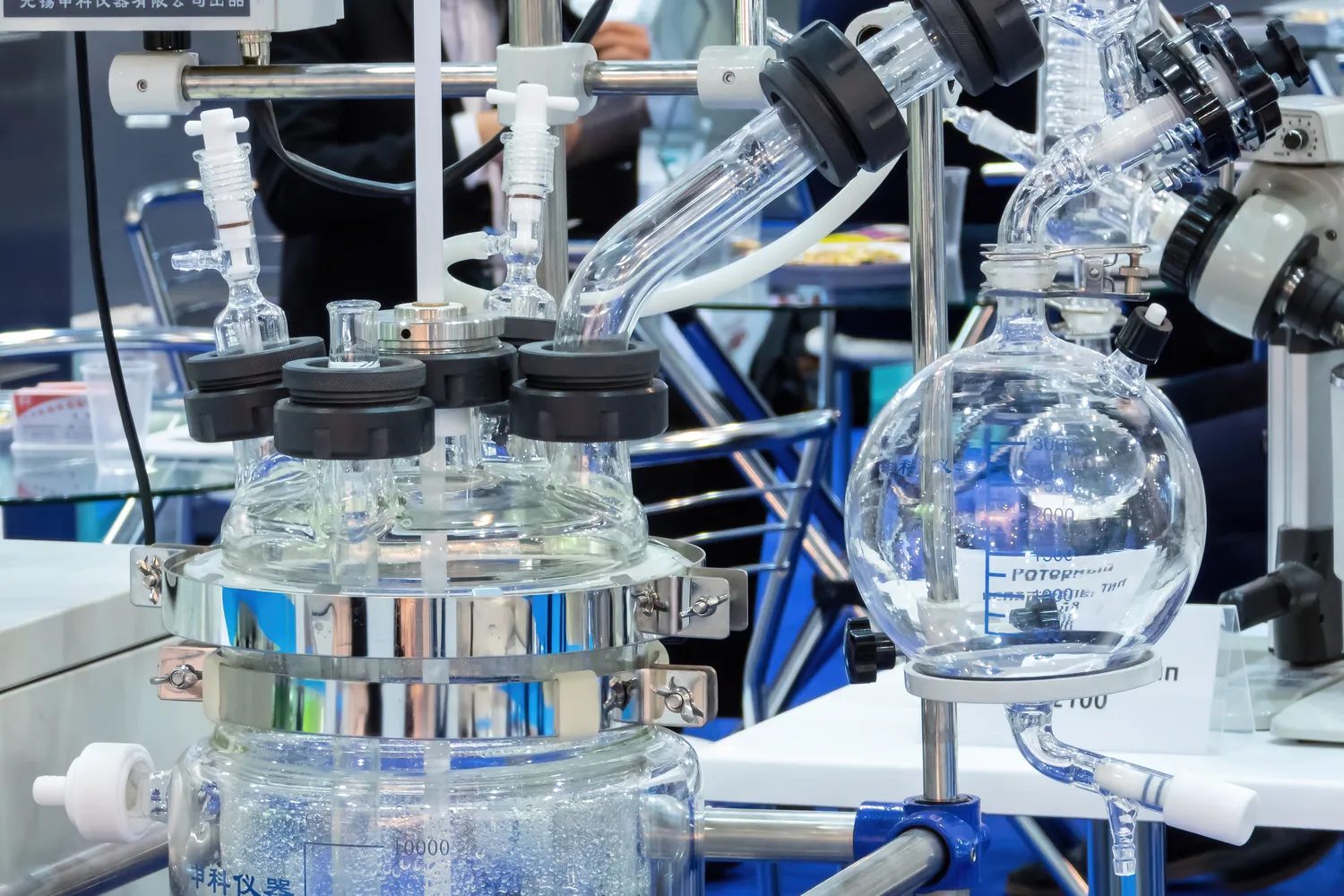
Budowa destylatora przemysłowego opiera się na kilku kluczowych elementach, które współpracują ze sobą w celu zapewnienia efektywnego procesu destylacji. Podstawowym komponentem jest zbiornik, w którym umieszczana jest ciecz do destylacji. Zbiornik ten jest zazwyczaj wyposażony w system grzewczy, który podgrzewa ciecz do odpowiedniej temperatury. Kolejnym istotnym elementem jest kolumna destylacyjna, która umożliwia separację składników na podstawie ich temperatur wrzenia. W kolumnie znajdują się różne elementy wspomagające proces separacji, takie jak wypełnienia czy tray’e, które zwiększają powierzchnię kontaktu między parą a cieczą. Po przejściu przez kolumnę para trafia do skraplacza, gdzie zostaje schłodzona i skondensowana z powrotem do stanu ciekłego. Ostatnim kluczowym elementem jest zbiornik odbiorczy, w którym gromadzi się gotowy produkt.
Jakie są najczęstsze problemy z działaniem destylatora przemysłowego
Podczas eksploatacji destylatora przemysłowego mogą wystąpić różnorodne problemy, które mogą wpływać na jego wydajność oraz jakość uzyskiwanych produktów. Jednym z najczęstszych problemów jest zatykanie kolumny destylacyjnej, co może prowadzić do obniżenia efektywności separacji składników. Zatykanie może być spowodowane osadami lub zanieczyszczeniami obecnymi w cieczy roboczej. Innym powszechnym problemem jest niewłaściwe zarządzanie temperaturą i ciśnieniem, co może prowadzić do nieefektywnej destylacji oraz obniżenia jakości produktu końcowego. Często zdarza się również problem z uszczelnieniami i połączeniami, które mogą prowadzić do wycieków substancji chemicznych lub pary wodnej. Dodatkowo niewłaściwe ustawienia parametrów pracy mogą skutkować powstawaniem niepożądanych produktów ubocznych lub zanieczyszczeń.
Jakie są zalety stosowania nowoczesnych destylatorów przemysłowych
Nowoczesne destylatory przemysłowe oferują szereg zalet, które przyczyniają się do zwiększenia efektywności procesów produkcyjnych oraz poprawy jakości uzyskiwanych produktów. Przede wszystkim nowoczesne technologie pozwalają na osiągnięcie wyższej czystości produktów dzięki zastosowaniu zaawansowanych metod separacji oraz automatyzacji procesów. Dzięki temu możliwe jest ograniczenie strat surowców oraz minimalizacja generowanych odpadów. Ponadto nowoczesne destylatory charakteryzują się większą energooszczędnością dzięki zastosowaniu innowacyjnych rozwiązań technologicznych, takich jak odzysk ciepła czy optymalizacja procesów grzewczych. Wiele z tych urządzeń jest również wyposażonych w systemy monitoringu i kontroli parametrów pracy, co pozwala na bieżąco śledzenie efektywności procesu oraz szybką reakcję na ewentualne problemy. Dodatkowo nowoczesne rozwiązania często uwzględniają aspekty ekologiczne poprzez zmniejszenie emisji substancji szkodliwych oraz zużycia energii.
Jakie są różnice między destylatorami przemysłowymi a laboratoryjnymi
Destylatory przemysłowe i laboratoryjne różnią się pod wieloma względami, co wynika z ich przeznaczenia oraz skali działania. Destylatory przemysłowe są zaprojektowane do pracy na dużą skalę, co oznacza, że mogą przetwarzać znacznie większe ilości cieczy w krótszym czasie. Z tego powodu ich konstrukcja jest bardziej masywna i często wyposażona w zaawansowane systemy automatyzacji, które umożliwiają monitorowanie i kontrolowanie procesów w czasie rzeczywistym. W przeciwieństwie do tego, destylatory laboratoryjne są zazwyczaj mniejsze i służą do przeprowadzania eksperymentów oraz badań naukowych. Ich budowa jest bardziej elastyczna, co pozwala na łatwe dostosowywanie do różnych warunków eksperymentalnych. Kolejną istotną różnicą jest jakość uzyskiwanych produktów; destylatory przemysłowe muszą spełniać określone normy jakościowe, podczas gdy laboratoria mogą skupić się na badaniach czystości i właściwości substancji.
Jakie są najważniejsze czynniki wpływające na efektywność destylatora przemysłowego
Efektywność destylatora przemysłowego zależy od wielu czynników, które mogą znacząco wpłynąć na jakość procesu oraz uzyskiwanych produktów. Pierwszym z nich jest temperatura, która musi być precyzyjnie kontrolowana, aby zapewnić optymalne warunki dla separacji składników. Zbyt wysoka lub zbyt niska temperatura może prowadzić do nieefektywnej destylacji oraz obniżenia jakości produktu końcowego. Kolejnym kluczowym czynnikiem jest ciśnienie, które również powinno być monitorowane i regulowane w zależności od specyfiki procesu. Warto również zwrócić uwagę na rodzaj używanej kolumny destylacyjnej; jej konstrukcja oraz zastosowane materiały mają ogromny wpływ na efektywność separacji. Dodatkowo jakość surowców używanych w procesie ma znaczenie; zanieczyszczenia mogą wpływać na wydajność i czystość uzyskiwanych produktów. Ostatnim istotnym czynnikiem jest regularne utrzymanie urządzenia, które pozwala na uniknięcie problemów związanych z zatykanie kolumn czy uszkodzeniami mechanicznymi.
Jakie są najnowsze technologie w dziedzinie destylacji przemysłowej
W ostatnich latach w dziedzinie destylacji przemysłowej pojawiło się wiele innowacyjnych technologii, które znacząco poprawiają efektywność procesów produkcyjnych oraz jakość uzyskiwanych produktów. Jednym z najważniejszych trendów jest rozwój systemów automatyzacji i monitoringu, które pozwalają na bieżące śledzenie parametrów pracy destylatora oraz szybką reakcję na ewentualne problemy. Dzięki zastosowaniu sztucznej inteligencji i algorytmów uczenia maszynowego możliwe jest optymalizowanie procesów w czasie rzeczywistym, co przekłada się na zwiększenie wydajności i redukcję kosztów operacyjnych. Innym ważnym kierunkiem rozwoju są technologie odzysku ciepła, które pozwalają na zmniejszenie zużycia energii poprzez wykorzystanie ciepła generowanego podczas procesu destylacji do podgrzewania innych części instalacji. Również rozwój materiałów o wysokiej odporności chemicznej oraz termicznej przyczynia się do zwiększenia trwałości urządzeń oraz ich efektywności.
Jakie są zastosowania destylatorów przemysłowych w różnych branżach
Destylatory przemysłowe znajdują szerokie zastosowanie w różnych branżach, co sprawia, że są one niezwykle istotnym elementem wielu procesów produkcyjnych. W przemyśle chemicznym służą do produkcji różnorodnych substancji chemicznych, takich jak rozpuszczalniki czy kwasy, a także do oczyszczania surowców przed dalszym przetwarzaniem. W branży petrochemicznej destylatory są kluczowe w procesie rafinacji ropy naftowej, gdzie umożliwiają oddzielanie poszczególnych frakcji paliwowych oraz innych produktów pochodnych. W przemyśle spożywczym destylatory wykorzystywane są do produkcji alkoholu oraz ekstraktów smakowych; dzięki precyzyjnej kontroli procesu możliwe jest uzyskanie wysokiej jakości produktów o pożądanych właściwościach organoleptycznych. Również w sektorze farmaceutycznym destylacja odgrywa ważną rolę w produkcji leków oraz substancji czynnych; tutaj szczególnie istotna jest czystość uzyskiwanych produktów oraz zgodność z rygorystycznymi normami jakościowymi.
Jakie są koszty eksploatacji destylatora przemysłowego
Koszty eksploatacji destylatora przemysłowego mogą być znaczne i zależą od wielu czynników związanych zarówno z jego budową, jak i sposobem użytkowania. Przede wszystkim należy uwzględnić koszty energii potrzebnej do podgrzewania cieczy oraz utrzymania odpowiednich parametrów pracy urządzenia. W przypadku dużych instalacji przemysłowych zużycie energii może stanowić znaczną część całkowitych kosztów operacyjnych. Kolejnym istotnym elementem są koszty surowców; jakość używanej cieczy roboczej ma bezpośredni wpływ na efektywność procesu oraz jakość uzyskiwanego produktu końcowego. Dodatkowo należy pamiętać o kosztach związanych z konserwacją i naprawami urządzenia; regularne przeglądy techniczne są niezbędne dla zapewnienia długotrwałej i bezawaryjnej pracy destylatora. Koszty te mogą być różne w zależności od rodzaju stosowanych materiałów oraz technologii produkcji.
Jakie są przyszłe kierunki rozwoju technologii destylacji przemysłowej
Przyszłość technologii destylacji przemysłowej wydaje się obiecująca dzięki ciągłemu postępowi technologicznemu oraz rosnącym wymaganiom rynku dotyczących efektywności energetycznej i jakości produktów. Jednym z głównych kierunków rozwoju będzie dalsza automatyzacja procesów produkcyjnych; inteligentne systemy zarządzania będą mogły analizować dane w czasie rzeczywistym i optymalizować parametry pracy urządzeń bez interwencji ludzkiej. Również rozwój technologii odzysku ciepła stanie się kluczowy dla zmniejszenia kosztów operacyjnych oraz ograniczenia negatywnego wpływu na środowisko naturalne. W miarę wzrostu świadomości ekologicznej społeczeństw coraz większą rolę będą odgrywać technologie przyjazne dla środowiska; nowe metody separacji oparte na membranach czy nanotechnologii mogą stać się alternatywą dla tradycyjnej destylacji chemicznej. Dodatkowo rozwój materiałów o wysokiej odporności chemicznej może przyczynić się do zwiększenia trwałości urządzeń oraz ich efektywności operacyjnej.