Budowa maszyn pneumatycznych opiera się na kilku kluczowych elementach, które współdziałają ze sobą w celu zapewnienia efektywności i niezawodności działania. Na początku warto zwrócić uwagę na kompresor, który jest sercem systemu pneumatycznego. Jego zadaniem jest sprężanie powietrza, co pozwala na uzyskanie odpowiedniego ciśnienia niezbędnego do pracy innych komponentów. Kolejnym istotnym elementem jest zbiornik powietrza, który gromadzi sprężone powietrze i zapewnia jego dostępność w momencie, gdy maszyna tego potrzebuje. Warto również wspomnieć o zaworach, które kontrolują przepływ powietrza w systemie. Dzięki nim możliwe jest precyzyjne sterowanie działaniem maszyny oraz jej poszczególnych części. Nie można zapomnieć o siłownikach pneumatycznych, które przekształcają energię sprężonego powietrza w ruch mechaniczny. Siłowniki te są kluczowe w wielu aplikacjach przemysłowych, gdzie wymagane jest wykonywanie różnych zadań, takich jak podnoszenie, przesuwanie czy zaciskanie. Ostatnim ważnym elementem są przewody i złącza, które łączą wszystkie komponenty i umożliwiają swobodny przepływ powietrza w systemie.
Jakie zastosowania mają maszyny pneumatyczne w przemyśle
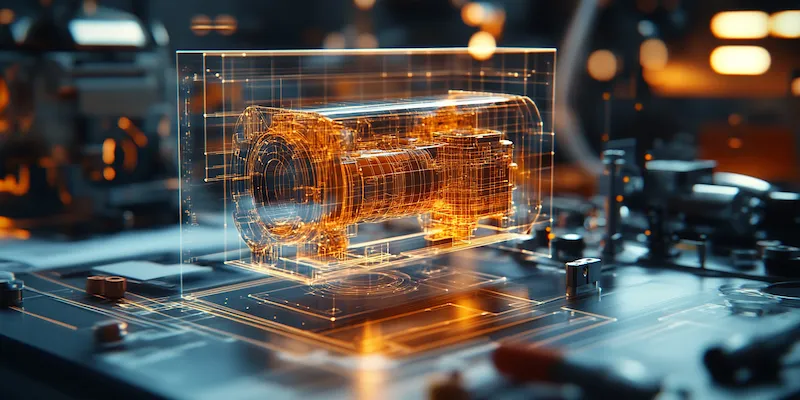
Maszyny pneumatyczne znajdują szerokie zastosowanie w różnych branżach przemysłowych dzięki swojej wszechstronności oraz efektywności działania. W sektorze produkcyjnym często wykorzystuje się je do automatyzacji procesów, co pozwala na zwiększenie wydajności oraz redukcję kosztów pracy. Przykładem mogą być linie montażowe, gdzie siłowniki pneumatyczne są używane do precyzyjnego manipulowania elementami oraz ich montażu. W branży spożywczej maszyny pneumatyczne służą do pakowania produktów, co zapewnia szybkie i higieniczne procesy. Dodatkowo w przemyśle motoryzacyjnym wykorzystywane są do malowania oraz obróbki powierzchni, co pozwala na uzyskanie wysokiej jakości wykończenia. W sektorze budowlanym maszyny pneumatyczne znajdują zastosowanie przy wierceniu otworów czy też przy rozbiórkach, gdzie ich moc i precyzja są nieocenione. Warto również zauważyć, że maszyny te są stosowane w systemach transportowych, gdzie sprężone powietrze napędza różnego rodzaju przenośniki oraz urządzenia transportowe.
Jakie są zalety i wady budowy maszyn pneumatycznych
Budowa maszyn pneumatycznych niesie ze sobą wiele zalet, które przyciągają inwestorów oraz inżynierów zajmujących się projektowaniem systemów automatyki. Jedną z głównych zalet jest ich prostota konstrukcji, co przekłada się na łatwość montażu oraz konserwacji. Systemy pneumatyczne charakteryzują się również dużą niezawodnością oraz długowiecznością, co sprawia, że są one idealnym rozwiązaniem dla przemysłu wymagającego ciągłej pracy bez awarii. Ponadto maszyny te działają cicho i nie emitują zanieczyszczeń chemicznych, co czyni je bardziej ekologicznymi niż inne systemy napędowe. Z drugiej strony istnieją także pewne wady związane z budową maszyn pneumatycznych. Jedną z nich jest ograniczona moc w porównaniu do systemów hydraulicznych czy elektrycznych, co może być problemem w przypadku bardziej wymagających aplikacji. Dodatkowo sprężone powietrze może być kosztowne w produkcji i wymaga odpowiednich instalacji do jego transportu oraz przechowywania. Warto również pamiętać o konieczności regularnej konserwacji układów pneumatycznych, aby uniknąć problemów związanych z nieszczelnością czy zużyciem komponentów.
Jakie innowacje wpływają na rozwój maszyn pneumatycznych
W ostatnich latach rozwój technologii przyczynił się do znacznych innowacji w dziedzinie budowy maszyn pneumatycznych. Jednym z najważniejszych trendów jest automatyzacja procesów produkcyjnych, która pozwala na zwiększenie efektywności działania maszyn oraz redukcję kosztów operacyjnych. Nowoczesne systemy sterowania umożliwiają precyzyjne monitorowanie parametrów pracy maszyn oraz dostosowywanie ich do zmieniających się warunków produkcji. Kolejnym istotnym aspektem jest rozwój materiałów stosowanych w budowie komponentów pneumatycznych. Dzięki nowoczesnym technologiom możliwe jest tworzenie lżejszych i bardziej wytrzymałych elementów, co wpływa na ogólną wydajność systemu. Innowacje dotyczą także technologii sprężania powietrza, gdzie nowe rozwiązania pozwalają na uzyskanie wyższej efektywności energetycznej oraz mniejszego zużycia energii podczas pracy maszyn. Również rozwój inteligentnych czujników i systemów monitorujących pozwala na bieżące śledzenie stanu technicznego maszyn oraz szybką reakcję na ewentualne awarie czy nieprawidłowości w działaniu.
Jakie są najczęstsze problemy w budowie maszyn pneumatycznych
W trakcie eksploatacji maszyn pneumatycznych mogą występować różne problemy, które wpływają na ich wydajność oraz niezawodność. Jednym z najczęściej spotykanych problemów jest nieszczelność układu pneumatycznego. Może to być spowodowane zużyciem uszczelek, pęknięciami w przewodach lub niewłaściwym montażem elementów. Nieszczelności prowadzą do utraty ciśnienia, co z kolei obniża efektywność działania maszyny i zwiększa koszty eksploatacji. Kolejnym problemem, który może wystąpić, jest zanieczyszczenie sprężonego powietrza. Zanieczyszczenia mogą pochodzić z otoczenia lub z samego układu, co prowadzi do uszkodzenia komponentów oraz obniżenia jakości pracy maszyn. Warto również zwrócić uwagę na niewłaściwe ustawienia ciśnienia roboczego, które mogą prowadzić do nieprawidłowego działania siłowników oraz innych elementów systemu. Często występującym problemem są także awarie zaworów, które mogą być spowodowane ich zużyciem lub zanieczyszczeniem.
Jakie są koszty związane z budową maszyn pneumatycznych
Koszty związane z budową maszyn pneumatycznych mogą się znacznie różnić w zależności od zastosowania, skomplikowania systemu oraz jakości użytych komponentów. Na początku warto uwzględnić koszty zakupu poszczególnych elementów, takich jak kompresory, zbiorniki powietrza, siłowniki czy zawory. Wysokiej jakości komponenty często wiążą się z wyższymi kosztami początkowymi, ale mogą przynieść oszczędności w dłuższej perspektywie dzięki większej niezawodności i mniejszym kosztom eksploatacyjnym. Dodatkowo należy uwzględnić koszty instalacji systemu oraz ewentualnych prac montażowych, które mogą być znaczące w przypadku bardziej skomplikowanych układów. Koszty związane z konserwacją i serwisowaniem maszyn również powinny być brane pod uwagę, ponieważ regularne przeglądy i wymiana zużytych części są kluczowe dla zapewnienia długotrwałego działania systemu. Warto również pamiętać o kosztach energii elektrycznej potrzebnej do zasilania kompresorów, które mogą stanowić istotny element całkowitych wydatków operacyjnych.
Jakie są przyszłe kierunki rozwoju technologii maszyn pneumatycznych
Przyszłość technologii maszyn pneumatycznych zapowiada się obiecująco dzięki dynamicznemu rozwojowi innowacji oraz rosnącym wymaganiom rynku przemysłowego. Jednym z kluczowych kierunków rozwoju jest integracja systemów pneumatycznych z technologiami cyfrowymi i Internetem Rzeczy (IoT). Dzięki temu możliwe będzie zbieranie danych dotyczących pracy maszyn w czasie rzeczywistym oraz ich analiza, co pozwoli na optymalizację procesów produkcyjnych oraz szybsze wykrywanie potencjalnych problemów. Kolejnym istotnym trendem jest rozwój bardziej zaawansowanych materiałów i komponentów, które będą charakteryzować się większą wytrzymałością oraz odpornością na działanie wysokich temperatur czy agresywnych substancji chemicznych. Innowacje te przyczynią się do zwiększenia efektywności energetycznej systemów pneumatycznych oraz ich dłuższej żywotności. Również automatyzacja procesów produkcyjnych będzie odgrywać coraz większą rolę w rozwoju technologii pneumatycznych, co pozwoli na dalsze zwiększenie wydajności oraz redukcję kosztów operacyjnych.
Jakie są różnice między maszynami pneumatycznymi a hydraulicznymi
Maszyny pneumatyczne i hydrauliczne to dwa różne typy systemów napędowych stosowanych w przemyśle, które mają swoje unikalne cechy oraz zastosowania. Główna różnica między nimi polega na medium roboczym – maszyny pneumatyczne wykorzystują sprężone powietrze jako źródło energii, podczas gdy maszyny hydrauliczne korzystają z cieczy hydraulicznych, takich jak oleje czy płyny hydrauliczne. To sprawia, że maszyny pneumatyczne są zazwyczaj lżejsze i prostsze w budowie niż ich hydrauliczne odpowiedniki. Pneumatyka charakteryzuje się również szybszymi reakcjami na zmiany ciśnienia oraz łatwiejszymi możliwościami regulacji przepływu powietrza przez zawory. Z drugiej strony maszyny hydrauliczne oferują znacznie większą moc i moment obrotowy przy mniejszych rozmiarach jednostek napędowych, co czyni je bardziej odpowiednimi do ciężkich zastosowań przemysłowych wymagających dużych sił roboczych. Ponadto systemy hydrauliczne są bardziej odporne na zmiany temperatury otoczenia i mają lepszą zdolność do przenoszenia obciążeń statycznych.
Jakie są kluczowe zasady bezpieczeństwa przy pracy z maszynami pneumatycznymi
Bezpieczeństwo pracy z maszynami pneumatycznymi jest niezwykle istotne zarówno dla operatorów, jak i dla całego zakładu produkcyjnego. Kluczową zasadą jest przestrzeganie norm BHP oraz stosowanie odpowiednich środków ochrony osobistej, takich jak kaski, rękawice czy okulary ochronne. Ważne jest również regularne szkolenie pracowników dotyczące obsługi maszyn oraz procedur bezpieczeństwa związanych z ich użytkowaniem. Przed rozpoczęciem pracy należy zawsze przeprowadzić dokładną inspekcję sprzętu w celu wykrycia ewentualnych uszkodzeń lub nieszczelności w układzie pneumatycznym. Należy również upewnić się, że wszystkie zawory są prawidłowo ustawione przed uruchomieniem maszyny. W przypadku wystąpienia jakichkolwiek nieprawidłowości należy natychmiast przerwać pracę i zgłosić problem przełożonemu lub technikowi serwisowemu. Ważnym aspektem bezpieczeństwa jest także odpowiednie oznakowanie strefy pracy wokół maszyn pneumatycznych oraz zapewnienie dostępu do instrukcji obsługi w widocznych miejscach.