Budowa maszyn specjalnych to złożony proces, który wymaga uwzględnienia wielu kluczowych elementów. Przede wszystkim, projektowanie takich maszyn zaczyna się od analizy potrzeb użytkowników oraz specyfikacji technicznych, które określają, jakie funkcje maszyna ma pełnić. W tym etapie ważne jest zrozumienie, w jakich warunkach maszyna będzie pracować oraz jakie zadania ma realizować. Kolejnym krokiem jest dobór odpowiednich materiałów, które zapewnią trwałość i niezawodność urządzenia. W przypadku maszyn specjalnych często stosuje się materiały kompozytowe lub stopy metali, które charakteryzują się wysoką wytrzymałością i odpornością na różne czynniki zewnętrzne. Następnie następuje etap projektowania mechanizmów, które będą napędzać maszynę oraz jej systemów sterowania. W tym kontekście istotne jest zastosowanie nowoczesnych technologii, takich jak automatyka czy robotyka, które pozwalają na zwiększenie efektywności i precyzji działania maszyny.
Jakie technologie są wykorzystywane w budowie maszyn specjalnych
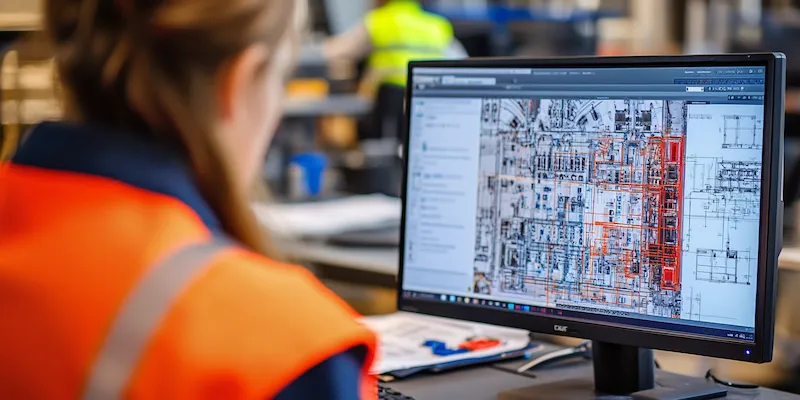
W budowie maszyn specjalnych wykorzystywane są różnorodne technologie, które mają na celu zwiększenie efektywności produkcji oraz poprawę jakości finalnego produktu. Jedną z najważniejszych technologii jest modelowanie 3D, które pozwala inżynierom na wizualizację projektu przed jego realizacją. Dzięki temu można szybko wprowadzać zmiany i poprawki, co znacząco przyspiesza proces projektowania. Inną istotną technologią jest wykorzystanie symulacji komputerowych do analizy zachowań maszyny w różnych warunkach pracy. Takie podejście umożliwia przewidywanie potencjalnych problemów oraz optymalizację konstrukcji jeszcze przed rozpoczęciem produkcji. W ostatnich latach coraz większą rolę odgrywają również technologie związane z automatyzacją i robotyzacją procesów produkcyjnych. Dzięki zastosowaniu robotów przemysłowych możliwe jest zwiększenie wydajności oraz redukcja błędów ludzkich.
Jakie są najczęstsze zastosowania maszyn specjalnych w przemyśle
Maszyny specjalne znajdują szerokie zastosowanie w różnych branżach przemysłu, co sprawia, że ich budowa i projektowanie są niezwykle istotne dla rozwoju technologii. W przemyśle budowlanym często wykorzystywane są maszyny do robót ziemnych, takie jak koparki czy ładowarki, które ułatwiają wykonywanie ciężkich prac związanych z przygotowaniem terenu pod inwestycje budowlane. W sektorze produkcyjnym maszyny specjalne służą do automatyzacji procesów montażowych oraz pakujących, co pozwala na zwiększenie wydajności linii produkcyjnej oraz obniżenie kosztów pracy. W branży spożywczej maszyny te są wykorzystywane do przetwarzania żywności oraz pakowania produktów, co ma kluczowe znaczenie dla zapewnienia wysokiej jakości i bezpieczeństwa żywności. Również w medycynie maszyny specjalne odgrywają istotną rolę; przykładem mogą być urządzenia do diagnostyki obrazowej czy roboty chirurgiczne, które zwiększają precyzję zabiegów medycznych.
Jakie wyzwania stoją przed inżynierami przy budowie maszyn specjalnych
Inżynierowie zajmujący się budową maszyn specjalnych napotykają wiele wyzwań, które mogą wpłynąć na przebieg całego procesu projektowania i produkcji. Jednym z największych problemów jest konieczność dostosowania się do szybko zmieniających się potrzeb rynku oraz oczekiwań klientów. Klienci często wymagają innowacyjnych rozwiązań technologicznych oraz większej elastyczności w produkcie końcowym, co zmusza inżynierów do ciągłego poszerzania swojej wiedzy i umiejętności. Kolejnym wyzwaniem jest integracja różnych systemów i technologii w jedną spójną całość; często maszyny specjalne muszą współpracować z istniejącymi już rozwiązaniami w zakładzie produkcyjnym. Ponadto inżynierowie muszą zmagać się z ograniczeniami budżetowymi oraz czasowymi, co wymaga umiejętności efektywnego zarządzania projektem i zasobami. Nie można również zapominać o aspektach związanych z bezpieczeństwem pracy; każda maszyna musi spełniać rygorystyczne normy dotyczące ochrony zdrowia i życia pracowników.
Jakie są kluczowe etapy w procesie budowy maszyn specjalnych
Proces budowy maszyn specjalnych składa się z kilku kluczowych etapów, które są niezbędne do osiągnięcia zamierzonych celów projektowych. Pierwszym krokiem jest faza koncepcyjna, która polega na zbieraniu wymagań od przyszłych użytkowników oraz analizie rynku. W tym etapie inżynierowie muszą zrozumieć, jakie funkcje maszyna ma pełnić oraz jakie problemy ma rozwiązywać. Następnie przechodzi się do fazy projektowania, gdzie tworzone są wstępne szkice i modele 3D. W tej fazie istotne jest również dobieranie odpowiednich materiałów oraz technologii produkcji, co może mieć wpływ na późniejsze działanie maszyny. Po zakończeniu projektowania następuje etap prototypowania, gdzie budowany jest pierwszy model maszyny. Prototyp pozwala na testowanie różnych rozwiązań i wprowadzanie ewentualnych poprawek przed rozpoczęciem masowej produkcji. Kolejnym krokiem jest produkcja seryjna, która wymaga precyzyjnego planowania i organizacji pracy w zakładzie. Ostatnim etapem jest testowanie gotowej maszyny w warunkach rzeczywistych, co pozwala na weryfikację jej funkcjonalności oraz bezpieczeństwa.
Jakie umiejętności są niezbędne dla inżynierów zajmujących się budową maszyn specjalnych
Inżynierowie zajmujący się budową maszyn specjalnych muszą posiadać szereg umiejętności technicznych oraz interpersonalnych, które są niezbędne do skutecznego realizowania projektów. Przede wszystkim, kluczowa jest wiedza z zakresu mechaniki i inżynierii materiałowej, ponieważ to właśnie te dziedziny stanowią fundamenty projektowania maszyn. Inżynierowie powinni być również biegli w obsłudze programów CAD (Computer-Aided Design), które umożliwiają tworzenie precyzyjnych modeli 3D oraz rysunków technicznych. Umiejętność analizy danych oraz znajomość metod symulacji komputerowych są równie ważne, ponieważ pozwalają na przewidywanie zachowań maszyny w różnych warunkach pracy. Równie istotne są umiejętności związane z zarządzaniem projektem; inżynierowie muszą potrafić planować harmonogramy prac oraz efektywnie koordynować działania zespołu. Współpraca z innymi specjalistami wymaga także umiejętności komunikacyjnych oraz zdolności do pracy w grupie. W obliczu dynamicznych zmian technologicznych inżynierowie muszą być otwarci na ciągłe kształcenie się i rozwijanie swoich kompetencji, aby nadążać za nowinkami w branży.
Jakie są najnowsze trendy w budowie maszyn specjalnych
W ostatnich latach można zaobserwować wiele interesujących trendów w budowie maszyn specjalnych, które mają na celu zwiększenie efektywności produkcji oraz poprawę jakości produktów. Jednym z najważniejszych trendów jest automatyzacja procesów produkcyjnych; coraz więcej firm inwestuje w robotyzację linii montażowych, co pozwala na zwiększenie wydajności oraz redukcję kosztów pracy. W kontekście automatyzacji warto również wspomnieć o wykorzystaniu sztucznej inteligencji i uczenia maszynowego do optymalizacji procesów produkcyjnych oraz analizy danych. Dzięki tym technologiom możliwe jest przewidywanie awarii maszyn oraz planowanie działań serwisowych jeszcze przed wystąpieniem problemu. Kolejnym trendem jest zastosowanie technologii druku 3D w procesie produkcji części do maszyn specjalnych; ta innowacyjna metoda pozwala na szybkie prototypowanie oraz produkcję skomplikowanych elementów o niskich kosztach. Również zrównoważony rozwój staje się coraz ważniejszym aspektem w budowie maszyn; firmy starają się wdrażać rozwiązania ekologiczne i energooszczędne, co ma pozytywny wpływ na środowisko naturalne.
Jakie są kluczowe wyzwania związane z ekologiczną budową maszyn specjalnych
Ekologiczna budowa maszyn specjalnych stawia przed inżynierami wiele wyzwań, które wymagają innowacyjnego podejścia i przemyślanych rozwiązań. Przede wszystkim konieczne jest zminimalizowanie negatywnego wpływu procesu produkcji na środowisko naturalne; oznacza to m.in. ograniczenie emisji gazów cieplarnianych oraz zużycia energii i surowców. Inżynierowie muszą poszukiwać alternatywnych materiałów, które będą bardziej przyjazne dla środowiska i jednocześnie spełnią wymagania dotyczące trwałości i wytrzymałości konstrukcji. Ważnym aspektem jest także recykling komponentów maszyn; projektując nowe urządzenia, inżynierowie powinni uwzględniać możliwość ich późniejszego demontażu i ponownego wykorzystania materiałów. Kolejnym wyzwaniem jest dostosowanie procesów produkcyjnych do norm ekologicznych oraz standardów jakości; firmy muszą inwestować w technologie umożliwiające monitorowanie wpływu swojej działalności na środowisko i dostosowywać swoje działania do obowiązujących przepisów prawnych.
Jakie są perspektywy rozwoju branży budowy maszyn specjalnych
Perspektywy rozwoju branży budowy maszyn specjalnych są bardzo obiecujące, zwłaszcza w kontekście rosnącego zapotrzebowania na innowacyjne rozwiązania technologiczne w różnych sektorach przemysłu. W miarę jak firmy dążą do zwiększenia efektywności produkcji oraz poprawy jakości swoich produktów, rośnie znaczenie automatyzacji i robotyzacji procesów przemysłowych. To stwarza nowe możliwości dla producentów maszyn specjalnych, którzy mogą oferować zaawansowane technologie dostosowane do indywidualnych potrzeb klientów. Ponadto rozwój sztucznej inteligencji oraz Internetu Rzeczy (IoT) otwiera nowe horyzonty dla branży; maszyny stają się coraz bardziej inteligentne i zdolne do samodzielnego podejmowania decyzji na podstawie analizowanych danych. Warto również zauważyć rosnącą uwagę na kwestie ekologiczne; firmy zaczynają inwestować w technologie przyjazne dla środowiska, co może stać się kluczowym czynnikiem konkurencyjności na rynku. W związku z tym inżynierowie będą musieli dostosować swoje umiejętności do zmieniających się potrzeb rynku oraz rozwijać nowe kompetencje związane z ekologicznymi rozwiązaniami technologicznymi.